Blog
The latest nanoparticle articles from Nikalyte Ltd.
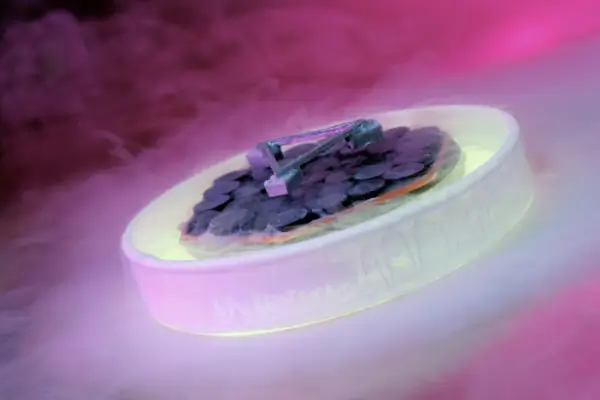
High-Temperature Superconductors Shaping the Future of Quantum Materials
Plasmonics, the study of light interacting with free electrons on metal surfaces, has become an essential tool for advancing quantum technologies. By exploiting the unique properties of plasmonic materials, typically metals such as gold, silver, and copper, researchers have opened new avenues for improving the sensitivity, precision, and capabilities of quantum systems. In particular, the
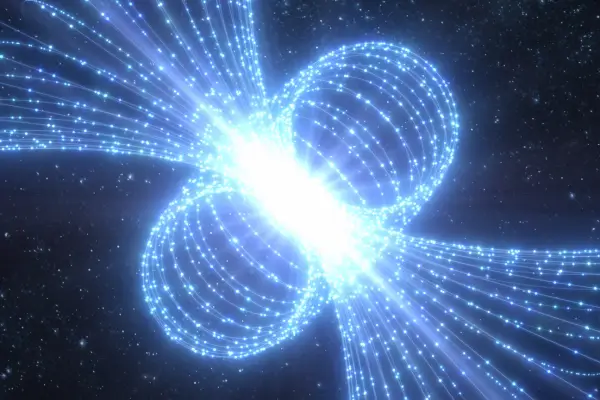
Plasmonic Interactions in Quantum Sensing Materials
Plasmonics, the study of light interacting with free electrons on metal surfaces, has become an essential tool for advancing quantum technologies. By exploiting the unique properties of plasmonic materials, typically metals such as gold, silver, and copper, researchers have opened new avenues for improving the sensitivity, precision, and capabilities of quantum systems. In particular, the
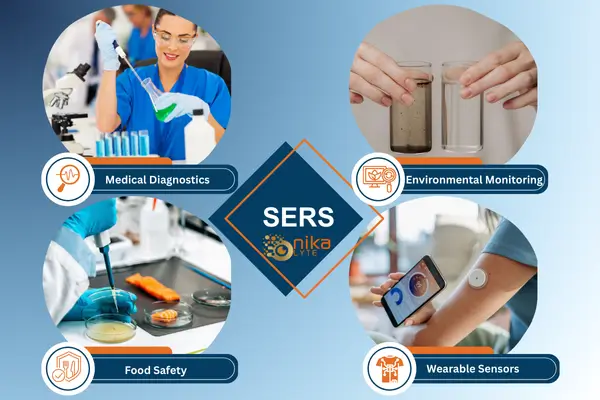
SERS for Biosensing Applications
Surface-Enhanced Raman Scattering (SERS) has rapidly gained recognition as a groundbreaking biosensing technique, enabling the accurate, rapid, and non-invasive detection of diseases, pathogens, and environmental toxins. By significantly amplifying Raman signals through nanomaterials, SERS makes it possible to detect trace amounts of biological analytes, positioning it as a leading method for medical diagnostics, food safety,
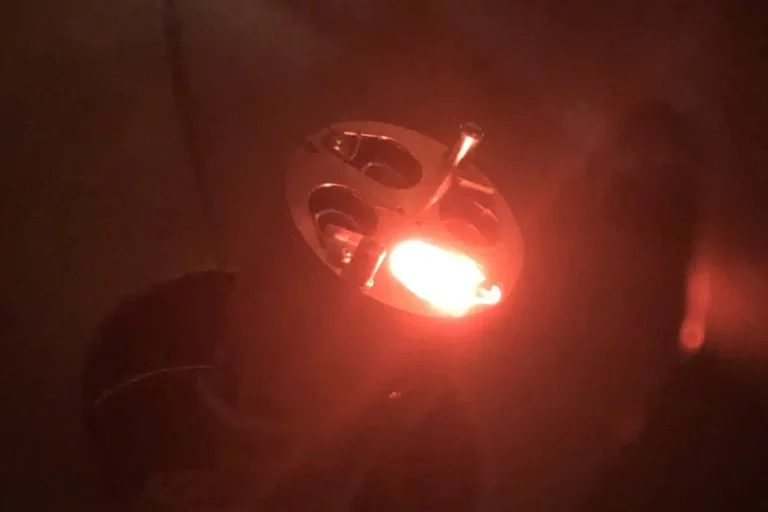
What is Electron Beam Evaporation?
Electron Beam Evaporation (E-Beam Evaporation) is a precise Physical Vapor Deposition (PVD) process used for applying high-density, thin coatings to substrates. E-Beam Evaporation operates under high vacuum conditions and employs a focused electron beam to evaporate the coating material (source material), which is then deposited onto a substrate.[1] This deposition method is essential for industries
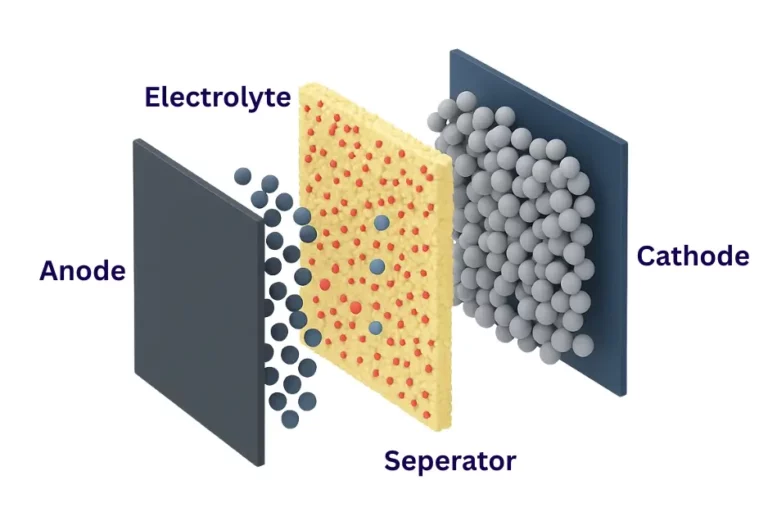
The Benefits of PVD for Chemical-Free Powder Coatings
Powder coating has become a preferred method for enhancing functionality and applying durable finishes to a variety of substrates, from automotive components to industrial machinery. However, the latest advancements in PVD (Physical Vapor Deposition) technology are transforming the way we think about coating processes. This innovative approach not only improves the quality and precision of
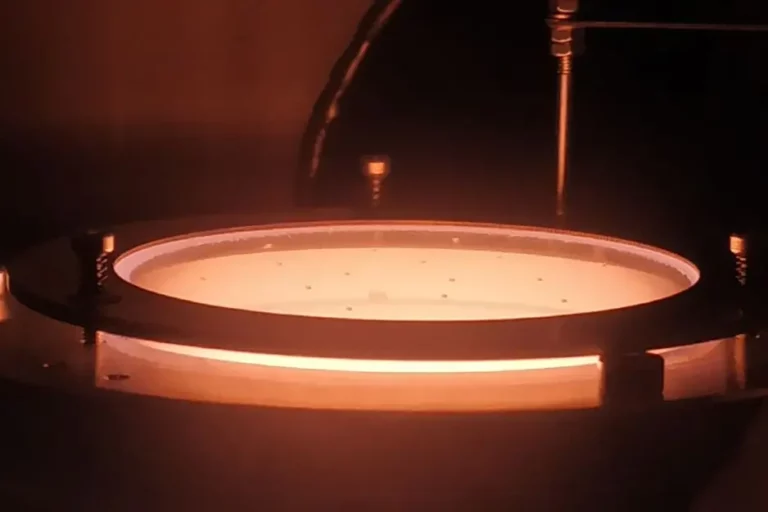
RF Atom Sources for UHV Epitaxy of Oxides & III-V Nitrides
In today’s race for faster, more efficient semiconductors and advanced electronic materials, true innovation begins at the atomic scale. Whether it’s next-generation optoelectronics, wide-bandgap power devices, or quantum materials, the performance of these technologies depends on the precision and purity of their thin-film layers. The RF (Radio Frequency) Atom Source has become a pivotal component
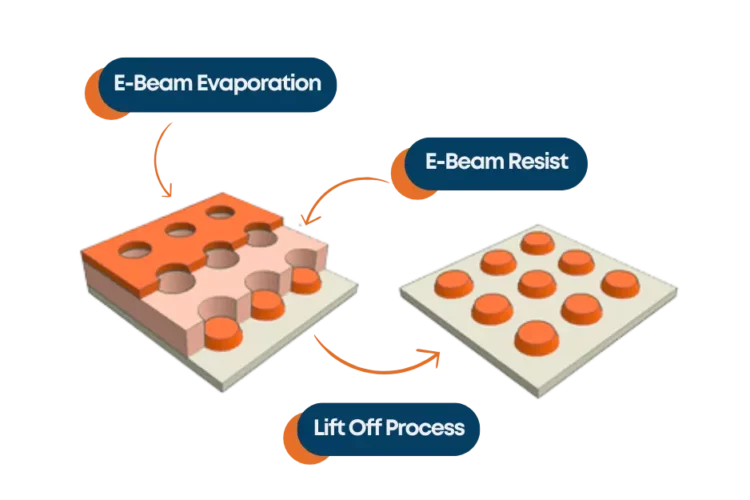
Lift-Off Process for Nanoscale Devices Using E-Beam Deposition
Image courtesy: Lift off process using E-beam deposition (adapted from Eschimese, D., Vaurette, F., Troadec, D., Leveque, G., Melin, T., and Arscott, S., “Size and shape control of a variety of metallic nanostructures using tilted, rotating evaporation and lithographic lift-off techniques,” Scientific Reports, 9, 14058, 2019, DOI: https://www.nature.com/articles/s41598-019-44074-w The lift-off process is one of the
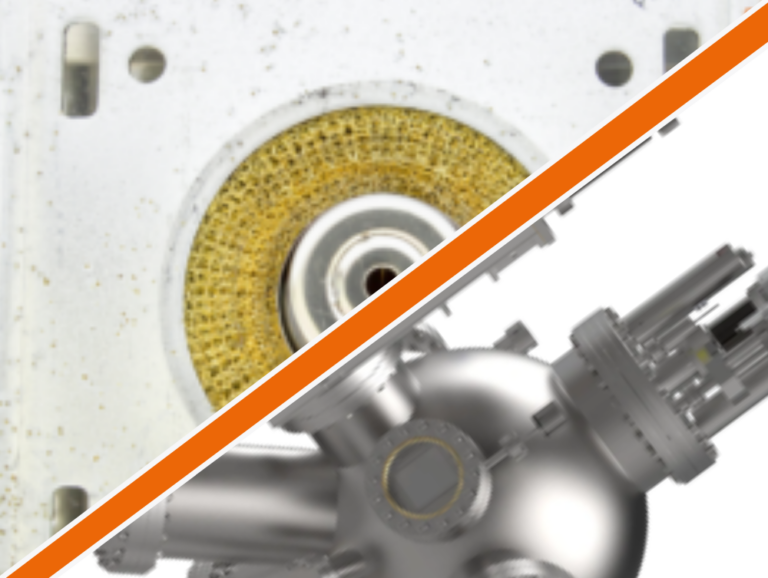
A practical guide to magnetron-based thin film deposition
Thin films are at the heart of modern technology, used in everything from semiconductor devices to optical coatings and protective layers. Magnetron-based thin film deposition is one of the most effective methods for producing high-quality coatings with exceptional uniformity, adhesion, and material control. By utilizing plasma to transfer material from a target onto a substrate,
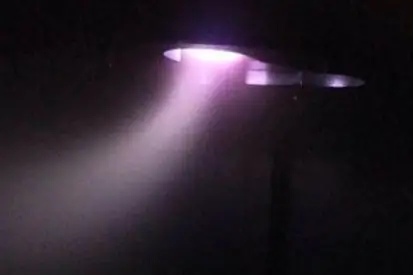
Superior thin film Coatings with Multi-Target Sputtering
In thin film deposition, precision and control are critical for producing high-performance coatings that meet the rigorous demands of industries such as semiconductors, optics, and materials science. Multi-target sputtering, particularly systems with three target configurations, has emerged as a transformative solution to enhance deposition versatility, material composition, and process control. The Need for Multi-Target Sputtering
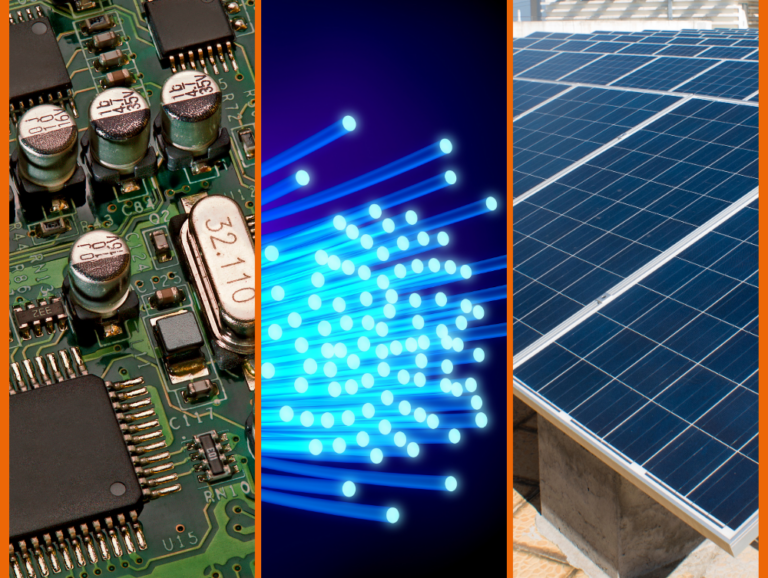
Why RF sputter deposition is used for dielectrics
Dielectric materials are the foundation of modern electronics, acting as insulators in circuits, capacitors, and semiconductor devices. Their ability to store and manage electric fields makes them indispensable in everything from microchips to high-frequency communication systems. However, producing high-quality dielectric films with the required precision and uniformity is a challenge. Among the thin-film deposition techniques,
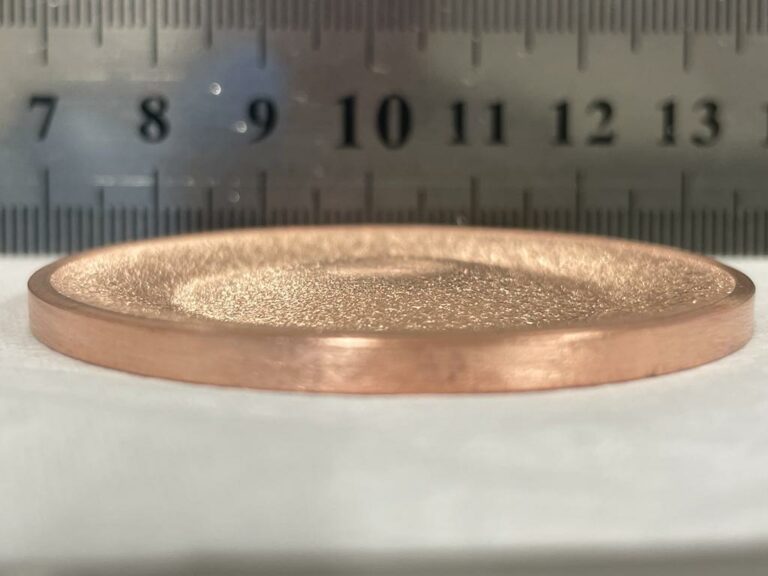
Exploring configuration options for magnetron sputtering equipment
Magnetron sputtering is a powerful thin-film deposition technique used in semiconductors, optics, and wear-resistant coatings. A magnetron sputtering system operates by generating a plasma that ejects atoms from a target material, which then deposit onto a substrate to form a thin film. While this fundamental process remains the same across applications, the configuration of a
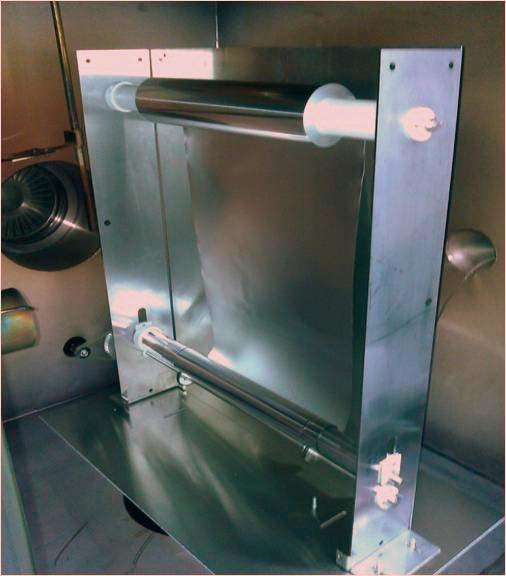
What to look for in scalable physical vapor deposition equipment
Choosing physical vapor deposition (PVD) equipment is a decision that extends beyond meeting current production needs. It requires thinking ahead to ensure the system you invest in today can support future expansion without costly overhauls. Industries relying on thin-film coatings, from semiconductors and optical technologies to medical devices and energy solutions, need physical vapor deposition