Surface engineering is an age-old custom. Yet it was only in the 1970s that we started achieving uniform microscopic coatings on substrates with any degree of efficiency. This is linked to the genesis of magnetron sputtering. We understood the basic physics of sputtering as early as the mid-19th Century, but it took almost a hundred years to leverage it in a coating process: direct current (DC) diode sputtering. Even then, the approach was hindered by extremely high costs and poor deposition rates. Radiofrequency (RF) sputtering showed promise during the ’60s, but it wasn’t until the magnetically enhanced version of diode sputtering was introduced that high-rate vacuum coating via sputtering really took off.So, how does it work?
In a typical setup, a magnetron uses a specially shaped magnetic field applied to a sputtering target. This magnetic field helps trap electrons in localized regions close to the target, increasing the probability of collisions with gas atoms and enhancing ionization efficiency. The increased ionization improves sputtering rates and deposition efficiency. The magnetron design ensures that the plasma is localized in front of the target, creating a characteristic erosion groove as the target material wears away. The erosion profile is crucial in determining target utilization, which typically ranges from 20% to 50%, depending on the magnetron design.Magnetron sputtering has several advantages over other vacuum coating techniques like thermal evaporation or diode sputtering. It offers higher deposition rates, the ability to easily sputter metals, alloys, and compounds, high-purity films, and excellent uniformity on large-area substrates. These properties make it a preferred choice for high-stakes applications in electronics, optics, and more.
The Basics of Magnetron Sputtering
Magnetron sputtering is an advanced thin film deposition technique used across a range of materials science applications, from coating microelectronics to modifying material properties and adding decorative finishes. What sets magnetron sputtering apart from other forms of physical vapor deposition (PVD) is the use of a magnetic field and negatively charged cathode to trap electrons near the target. This helps engineers fabricate high-quality, thin films with superior adhesion and consistency.
How Does Magnetron Sputtering Deposition Work?
To start, the process requires a vacuum chamber that minimizes contamination and ensures a clean environment for coating. The vacuum also allows the ejected atoms to travel without interference, ensuring high-quality deposition. Once in a vacuum, an inert gas—typically argon—is introduced to serve as the sputtering medium. The system is energized with high voltage, which ionizes the argon atoms and creates a plasma. This plasma consists of positively charged ions that are accelerated toward the negatively charged target material.The target, acting as the cathode, is bombarded by the argon ions. The impact of these ions releases atoms from the target’s surface—a process called sputtering. The magnetic field generated by the magnetron serves to trap electrons near the target surface, increasing the ionization rate of the argon gas. This results in a higher density of plasma and more efficient sputtering.The dislodged atoms from the target material travel across the vacuum chamber and deposit onto the substrate, forming a thin film. The magnetic field’s design is essential in increasing the efficiency of ion production and controlling the uniformity of the coating. By confining the electrons to the target’s surface, the magnetron ensures that more ionizing collisions occur, which not only enhances the sputtering rate but also helps in creating a denser, more adherent film. Additionally, the configuration of the magnets can vary, such as planar or cylindrical magnetrons, to optimize the coating for different applications and substrate geometries.The mean free path of the atoms—essentially the average distance an atom can travel without colliding with other gas particles—plays a significant role in determining the effectiveness of the coating process. By maintaining low pressure in the vacuum chamber, magnetron sputtering ensures that the mean free path is long enough for the sputtered atoms to reach the substrate without losing energy. This allows for the production of high-quality films with precise control over thickness and properties, suitable for complex geometries and demanding applications.Why Choose Magnetron Sputtering?
When it comes to applying thin-film coatings, magnetron sputtering offers a number of compelling advantages:- Unmatched Uniformity and Adhesion: Magnetron sputtering’s precision allows for the creation of coatings with excellent adhesion and uniformity. Whether the application involves semiconductors, optics, or protective surfaces, these qualities are crucial for optimal performance.
- Material Versatility: One of magnetron sputtering’s strengths is its ability to handle a wide array of materials, from metals to ceramics and even some polymers. This versatility opens the door to diverse applications, including anti-reflective coatings, wear-resistant layers, and decorative finishes.
- Efficiency and Control: Thanks to the magnetic field, the process achieves higher deposition rates with less material waste, making it an efficient choice. The parameters, such as power and pressure, can be fine-tuned to meet specific thickness and property requirements, crucial for precision applications like microelectronics.
Applications Across Industries
The adaptability of magnetron sputtering has made it indispensable across numerous sectors:- Electronics: It’s widely used to deposit conductive and insulating layers in semiconductor devices, where uniformity and precision are paramount.
- Optics: Magnetron sputtering is frequently employed to create anti-reflective and mirror coatings, enhancing the performance and durability of optical components.
- Aerospace and Automotive: In these demanding industries, magnetron sputtering provides wear-resistant coatings that enhance the longevity and resilience of critical components.
- Medical Devices: The process even extends to the medical field, where biocompatible coatings on implants and surgical tools are essential for patient safety and device longevity.
Bringing It All Together: The Power of Magnetron Sputtering
Magnetron sputtering deposition is more than just a coating process—it’s a technology that drives innovation across various industries by enhancing product performance and durability. Whether it’s used to protect electronic components or create reflective optical films, magnetron sputtering’s precision and efficiency make it a standout in surface engineering.Curious to learn how magnetron sputtering can benefit your specific applications? Visit Nikalyte’s UHV Magnetron Sputter Sources page to explore our advanced PVD solutions and find the right fit for your needs.References and Further Reading
For more in-depth technical insights, see S. Swann’s article, ‘Magnetron Sputtering,’ published in Physics in Technology (1988).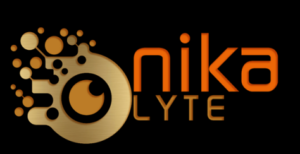