In the realm of material science and thin-film deposition, sputtering stands out as a pivotal technique for creating high-quality coatings. Whether you’re developing cutting-edge electronic devices, advanced optics, or high-performance sensors, the choice of sputtering technology can make a significant difference. In this blog post, we will discuss sputtering and explore how Nikalyte’s NEXUS and NL-FLEX PVD systems are can help you harness the art and science of sputtering.
What is Sputtering?
Sputtering is a physical vapor deposition (PVD) technique used to deposit thin films onto a variety of substrates. It involves ejecting material from a “target” source and depositing it onto a substrate in a vacuum chamber. The process begins when a high-energy plasma bombards the target material, knocking off atoms that then travel through the vacuum and condense on the substrate. [1]
Key benefits of sputtering include:
- Uniform Coatings: Achieves consistent thin film thickness across complex geometries.
- Material Versatility: Suitable for a wide range of materials, including metals, oxides, and nitrides.
- Precise Control: Offers excellent control over film thickness and composition.
Nikalyte’s PVD systems exemplify innovation in sputtering technology through our signature TGC Terminated Gas Condensation Sputtering technique. [2-3]
The TGC process combines sputtering and gas condensation techniques to produce high-quality nanoparticles. In this method, the target material is bombarded by energetic ions, to generate a vapour of metal atoms. This process takes place inside a special chamber called the aggregation zone, which is linked to the main sample chamber by a small aperture. A high pressure (10-1mbar) of argon gas inside the aggregation chamber causes the metal vapour to condenses to form clusters. The clusters grow to form nanoparticles as they travel through the aggregation zone and finally exit into the main sample chamber. The “terminated” aspect refers to controlling the gas environment during the condensation, allowing for enhanced material properties and improved uniformity. This approach is particularly useful in synthesizing complex materials like high-entropy alloys, enabling precise control over composition and microstructure
Our systems are designed to meet the demands of modern research and industrial applications with several standout features.
Nikalyte’s NEXUS: Ultra High Vacuum PVD system with Precision and Versatility
Engineered to deliver high-quality nanoparticles and thin film coatings, our product caters to both industrial and research applications across diverse fields such as catalysis, photonics, energy storage, sensors, and life sciences. It integrates effortlessly with analytical tools, which can be tailored to meet your unique research and production requirements.
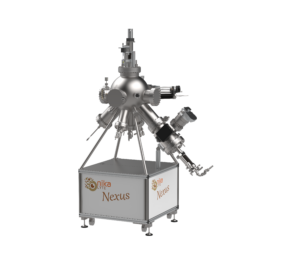
Highlights
- Advanced Control Systems: The NEXUS integrates state-of-the-art control systems that allow for fine-tuning of sputtering parameters. This precision ensures that coatings are applied uniformly and with the exact characteristics needed for specific applications.
- Enhanced Process Monitoring: The NEXUS is equipped with advanced diagnostic tools that provide real-time feedback on the sputtering process. This capability is crucial for maintaining high quality and reproducibility in coatings.
- User-Friendly Interface: Its intuitive interface makes it accessible to both novice and experienced users, streamlining the setup and operation of the system.
Nikalyte’s NL-FLEX: Modular PVD System with High-Throughput Sputtering
The NL-FLEX system is designed for high-throughput applications and stands out for its ability to handle multiple complex substrates simultaneously, including non-planar and planar surfaces, powder coating and reel-to-reel coatings, making it an ideal choice for n environments.
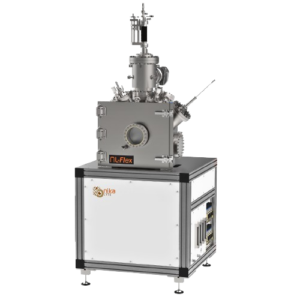
Highlights
- Flexible Substrate Configurations: With the ability to accommodate various substrate sizes and types, the NL-FLEX offers exceptional flexibility. This makes it ideal for both small-scale research projects and large-scale production runs.
- Scalability: The NL-FLEX is engineered to handle high-volume sputtering needs without compromising on quality. Its scalable design ensures that it can grow with your production requirements.
- Efficient Utilization of Targets: The system maximizes the use of target materials, reducing waste and lowering operational costs. This efficiency is achieved through advanced target rotation and positioning mechanisms.
- Rapid Process Cycle: With its fast-sputtering cycle times, the NL-FLEX minimizes downtime and accelerates production rates. This is particularly beneficial in industries where time-to-market is critical.
- Robust Automation: The NL-FLEX features extensive automation capabilities, including automated loading and unloading of substrates. This automation enhances productivity and reduces the need for manual intervention.
Applications and Benefits
Both the Nikalyte’s NEXUS and NL-FLEX systems cater to a range of applications, including:
- Electronics: For depositing conductive layers in semiconductors and other electronic components. [4]
- Biomedical Devices: In the medical field, thin-film coatings are used on implants and surgical instruments to improve biocompatibility and reduce the risk of infection. [5]
- Optics: For creating thin-film coatings that improve optical performance. [5]
- Catalysis: In chemical industries, nanoparticle coatings enhance the efficiency of catalysts used in various reactions, including those for energy production and environmental protection. [6,7]
- Sensors: Nanoparticle coatings improve the sensitivity and functionality of sensors used in various applications, from environmental monitoring to healthcare diagnostics. [6,7]
The combination of precision control, versatility, and efficiency offered by Nikalyte’s sputtering systems ensures that you can achieve high-quality nanoparticle and thin film coatings and ensures that you harness the art and science of sputtering.
Conclusion
Sputtering technology has come a long way, and with systems like the Nikalyte’s NEXUS and NL-FLEX , the future looks bright for those working with thin-film deposition and nanoparticle coatings. Whether you’re looking for precision in research or efficiency in production, these advanced sputtering systems provide the tools you need to push the boundaries of what’s possible and become an expert in the art and science of sputtering.
Stay tuned for more insights and updates on the latest in sputtering technology!
References
- Engineering LibreTexts – Sputtering
- Influence of source parameters on the growth of metal nanoparticles by sputter-gas-aggregation | Applied Nanoscience (springer.com)
- (PDF) Direct co-deposition of mono-sized nanoparticles during sputtering (researchgate.net)
- Recent Trends in Coatings and Thin Film: Modeling and Application
- Current Status, Challenges, and Future Prospects of Thin Film Coating Techniques
- Advances of Nanoparticles and Thin Films
- Thin Films/Properties and Applications