In thin film deposition, precision and control are critical for producing high-performance coatings that meet the rigorous demands of industries such as semiconductors, optics, and materials science. Multi-target sputtering, particularly systems with three target configurations, has emerged as a transformative solution to enhance deposition versatility, material composition, and process control.
The Need for Multi-Target Sputtering
Traditional single-target sputtering systems face significant limitations when it comes to creating coatings that require a combination of different materials or alloys. Each time a material change is needed, the process can be time-consuming and prone to inconsistencies. This is where multi-target sputtering systems come into play. By incorporating multiple targets into a single sputtering source, manufacturers can achieve faster transitions between materials, reducing downtime and improving overall efficiency. [1]
Moreover, multi-target sputtering provides enhanced control over film composition, allowing for precise adjustments in material ratios during co-sputtering. This capability is crucial for industries requiring coatings with specific and consistent material properties. The Tri Stellar Triple Target Sputter Source fully capitalizes on these advantages, offering superior flexibility and precision a single compact sputter source advanced multilayer and alloy thin film coatings.
Key Benefits of Multi-Target Sputtering
Enhanced Material Versatility:
The Tri Stellar Triple Target Sputter Source is engineered to simultaneously handle three distinct target materials in one compact UHV source. This capability enables the creation of multi-layered coatings with precise control over the composition of each layer. This feature is particularly beneficial for applications that require complex film stacks, such as optoelectronics, photovoltaics, and sensor technologies. [2]
Increased Process Efficiency:
A key advantage of the Tri Stellar system is its seamless transition between targets, eliminating the need for manual adjustments or system downtime. This results in reduced processing times and mitigates inconsistencies often introduced by target switching in traditional sputtering systems. The ability to operate continuously makes the system ideal for high-throughput production environments where speed and consistency are critical. [3]
Superior Film Quality:
Achieving high-quality coatings requires precise control over deposition parameters, including power, pressure, and target materials. The Tri Stellar system ensures enhanced uniformity even when sputtering from multiple targets, resulting in consistent film properties such as thickness, adhesion, and composition. This is essential for applications demanding top-tier performance in areas like semiconductors and optical coatings. [1]
Flexible Coating Designs:
The ability to simultaneously use three different target materials offers manufacturers the flexibility to experiment with advanced coating designs, such as gradient or composite films. Whether for optical coatings, protective layers, or multifunctional films, the Tri Stellar system allows for innovative material combinations without requiring separate processing steps, offering significant advantages in design flexibility. [4]
Real-World Applications of Multi-Target Sputtering
Semiconductor Devices:
Triple-target sputtering enables precise metal composition control for multilayer interconnects in integrated circuits, enhancing conductivity, minimizing resistance, and improving reliability in scaled-down microelectronic devices. [1]
High-K Dielectrics:
Advanced transistors, such as those used in FinFET or gate-all-around (GAA) technologies, require high-k dielectric materials for effective gate control. Triple-target sputtering facilitates the deposition of these complex dielectrics, enabling precise stoichiometry that improves the efficiency of next-generation semiconductor devices while reducing leakage currents. [5]
Antireflection Coatings:
By combining materials like silicon dioxide (SiO₂) and titanium dioxide (TiO₂), triple-target sputtering can achieve the high precision needed for antireflection coatings, crucial for optical devices such as lenses, sensors, and displays, ensuring better light transmission and minimal reflection. [6]
Optical Mirrors and Beam Splitters:
The ability to deposit multilayer thin films made from materials such as silver (Ag) and silicon nitride (Si₃N₄) enables the production of highly reflective and durable optical mirrors and beam splitters. These components are integral to high-performance optical systems, including laser systems and scientific instruments. [7]
Multilayer Hard Coatings:
Triple-target sputtering allows for the creation of multilayered coatings using materials like chromium nitride (CrN), titanium nitride (TiN), and niobium nitride (NbN). These coatings exhibit excellent hardness, high resistance to oxidation, and wear resistance, making them ideal for applications in cutting tools, aerospace components, and medical devices. [8]
Gradient Coatings:
The ability to create gradient coatings, where material properties gradually transition across the film, provides tools and industrial parts with optimal strength and toughness. This is especially valuable in components that endure significant mechanical stress and thermal cycling. [9]
Photovoltaic Absorber Layers:
In thin-film solar cells, such as copper indium gallium selenide (CIGS) technology, the ability to precisely control material composition is key to optimizing efficiency. Triple-target sputtering offers the flexibility needed to deposit CIGS films with the desired stoichiometry, improving energy conversion efficiency while minimizing material costs. [1]
Battery Electrodes:
For energy storage applications, particularly in lithium-ion batteries, the precise deposition of composite electrode materials is essential for improving charge/discharge cycles and overall battery performance. Triple-target magnetron sputtering enables precise deposition of composite electrode materials, improving conductivity, stability, and battery performance over extended cycles. [6]
Why Choose Nikalyte’s Triple-Target Magnetron Sputter Source
As the demand for advanced multi-material coatings grows, the Triple-Target Magnetron Sputter Source provides a unique solution to address these challenges. By enabling efficient multi-target sputtering, this tool enhances deposition precision, minimizes contamination risks, and offers improved control over film composition, essential for modern applications across a wide range of industries.
By integrating the Triple-Target Magnetron Sputter Source into your production line, you gain a flexible, high-performance tool capable of supporting next-generation device fabrication and material innovation. For detailed insights on how this technology can elevate your process, speak with one of our experts.
References:
- Cheng, Y., & Liu, L. (2007). Effect of target materials and gas pressure on the properties of TiO2 thin films prepared by multi-target sputtering. Surface and Coatings Technology, 201(23), 9296-9301. https://doi.org/10.1016/j.surfcoat.2007.04.016
- Triple Target Sputter Source: Tri Stellar. Nikalyte. Retrieved March 16, 2025, from https://www.nikalyte.com/triple-target-sputter-source-tri-stellar/
- Sputter target. ScienceDirect. Retrieved March 16, 2025, from https://www.sciencedirect.com/topics/engineering/sputter-target
- Zhang, X., & Yang, Y. (2020). Review on sputtering techniques for thin film deposition and applications. AIMS Materials Science, 7(3), 3484-3501. https://doi.org/10.3934/matersci.2020.3.3484
- Samsung SDI. (n.d.). Electronic materials. Samsung SDI. Retrieved March 16, 2025, from https://www.samsungsdi.com/business/electronic-materials.html
- Todorova, S., & Nedev, N. (2006). Deposition of thin films by magnetron sputtering: The effect of the magnetic field configuration. Journal of Magnetism and Magnetic Materials, 304(1), 141-146. https://doi.org/10.1016/j.jmmm.2006.03.031
- Sui, Q., Zhang, X., Chen, Y., & Liu, J. (2023). Development of ion-beam sputtered silicon nitride thin films for low-noise mirror coatings of gravitational wave detectors. ResearchGate. https://doi.org/10.13140/RG.2.2.26706.09927
- Keenan, D. T., & Bradley, J. W. (1999). A study of reactive magnetron sputtering: The effect of target material and sputtering conditions on thin film properties. Journal of Crystal Growth, 202(1-4), 1067-1076. https://doi.org/10.1016/S0040-6090(98)00992-4
- Yang, Y., & Chen, J. (2020). A review on the preparation and application of metal oxide thin films by sputtering. Journal of Crystal Growth, 541, 125729. https://doi.org/10.1016/j.jcrysgro.2020.125729
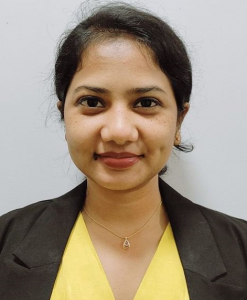